Think of the humble wire coat hanger - bend it once and it will not break, bend it ten times and it might not break but bend the coat hanger enough times and it will finally give!
The concept is known as Cycles-to-Failure.
The term is more commonly associated with cordage (rather than metal) but you get the general idea - each bend of the wire can be considered one cycle, with each cycle completed you are one step closer to breaking point.
Treevolution and Trudi & Partner TreeConsult stated back in 2008; "Metal is less prone to fatigue failure (in tree rigging operations) than cordage, and deformation is often easy to detect long before fracture occurs. Even so, if loads cannot be assessed precisely enough, it will not be possible to determine when the safe working load limit of rigging equipment has been exceeded."
Without getting too technical that's why a Safety (or Working Load) Factor is applied when using rope or hardware. (If you want to get a little more technical about safety factors and metal fatigue follow this link.
Here's what Samson have to say about working load factors relative to cordage but, for simplicities sake, the same can apply to hardware; "our recommendation, and one that is fairly well accepted in the industry, is a minimum of 10:1 working load factor for climbing lines and 5:1 working load factor for rigging lines (and hardware)."
In simple terms the higher the Safety Factor the greater the anticipated service life of the product. The longer the service life, the lower the replacement cost.
It makes good economic sense to apply a sensible Safety Factor to your rigging gear if you want a good return on your investment.
The failed ISC RP055 block below is the result, among other things, of too may cycles under heavy load, demonstrating metal fatigue in action.
The block would have gone through three distinct stages before the outer section of the back plate failed:
- hairline crack/fractures would have formed in areas of stress (at the base of the ridges in this instance)
- incremental extension or lengthening of the fracture over time (sometimes called crack propagation)
- ultimate failure when the crack/fracture reached sufficient length so that the remaining cross section could not support the load
The outer edges on the back plates of a rigging block experience the greatest stress during a rigging operation because they often connect violently with the stem while in use.
The front plates house the plate release mechanism. In order to protect the release mechanism, the block is configured so as not to come into direct contact with the stem.
This particular example would have had tiny hairline cracks running along the base of the ridge on the back plate before ultimate failure. These cracks may or may not have been visible to the naked eye.
The fractured section released when the block crashed to the ground, following the failure of the top strop. The block smashed, plate first, into a fallen log on the way down.
The moral of the story: pay careful attention to the condition and set of your top strop, the Safety Factor and Break Strength for all equipment in the system, be mindful of the number of heavy load cycles you apply and always scrutinize your rigging gear before use.
Retire equipment (hardware and software) if there are any signs of fatigue or you can expect the same result as below.
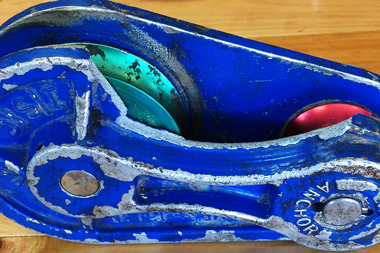